Light curing print model cannot adhere/easily falls off
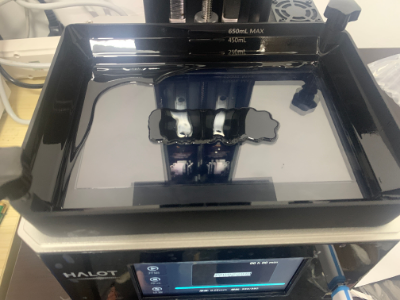
- Insufficient base exposure. When the platform is raised, the model will generate 2-sided tension from the adhesion of the release film and the platform. As the resin hardens and expands during exposure, it can fill all surfaces of the platform very tightly, so the actual adhesion surface of the platform is larger than the release film. The release film is coated and will separate first when raised. When the exposure is insufficient, the bonding effect of the adhesion area on the platform side is reduced, and the model can be separated from the platform.
- Platform too smooth. From factor one we know that the rougher the platform surface, the stronger the bonding effect. A too smooth platform cannot firmly grasp the bottom tension when the model resists lifting.
- The printing platform is not level. If the printing platform is not level, one side or corner of the platform may not stick together, and side tilt may cause printing to not start. The expression of factor one is that it is possible to leave the platform at any time during the printing process. According to this factor, as the exposure compensation continues, if the initial layer successfully adheres, the bottom in the upward direction may become thicker or separate more parts.
- The platform is not flat enough. Due to problems encountered by the printer during processing, most metal surfaces may become concave in the center if not treated. Slight deformation does not significantly affect model printing. In the case where the relative depression exceeds 1 millimeter, it is easy for the model to fall off. Especially the higher the printing layer, the higher the probability. When printing large layers, the bottom exposure in the middle is quite thick, the light cannot pass through, causing the resin on the platform surface to not harden or not fully harden. The model in the middle of the platform is more likely to drop.
- Material characteristics. Resin materials also affect the adhesion of the model. Special resins contain a lot of additives, which affect the curing effect. With the same exposure time, the bonding difficulty is greater. The "light-absorbing" ability of the resin's photosensitizer is too strong or too weak, which will also affect the curing effect.
- Slicing issues. ① There is too little support for model slicing, we need to add it again. On the other hand, the model itself is large, but the contact surface with the platform is small, resulting in the whole weight of the model increasing when printing to the second half, and the surface of the model attached to the platform is not enough to hold the whole model, so it will fall off. ② Add a base plate with a larger contact area, the whole modification can be printed again after completion. It should be noted that if the print fails, the resin should be filtered through a filter mesh before printing again to avoid the influence of model residues on the second print or even press the print screen.
- You can moderately increase the original exposure number by 2 seconds increments, up to about 100 (first layer exposure). Increase the first layer exposure count by increments of 1, up to 10 layers.
- Use low grit sandpaper or a hard object to roughen the print platform, the rougher it is, the better the adhesion.
- Re-level the print: Remove the material tray, loosen the screws on both sides of the platform, and click "return to origin" on the screen. Press the platform by hand, slightly tighten one set of diagonal screws first, not too tightly, then tighten the remaining two screws, and finally reinforce all once again. After reinforcement, you can use the light from your phone to see if light is leaking out from the two sides of the platform and the printing screen. If so, you need to repeat the above steps.
- You can use a straightedge to simply test the flatness or level of the print platform. If it is not flat, it is recommended to replace the print platform.
- Change to new consumables (for example, if the resin has been left idle for too long, or if it has expired, consider this aspect).
- Reslice. In the support settings of the slicing, the model can generate a base, and the base can increase the initial contact surface. By default, the base will be larger than the projected area of the model, so in multi-model slicing, we can horizontally move the models, so that the bases of the models are all connected together. This can effectively solve the risk of failure caused by the platform not being levelled well or being concave, and also avoid the situation of individual models falling off.
- The local temperature is too low, causing poor resin activity. You can soak the resin aluminum can in hot water for about ten minutes before using it.